We get our logs from European and American forests, researching the best quality plants for our Veneer production. The tree selection is made in order to give more light for the plants underneath it, giving new life to the younger ones.
Wooden veneers processing cycle
Selection of logs.
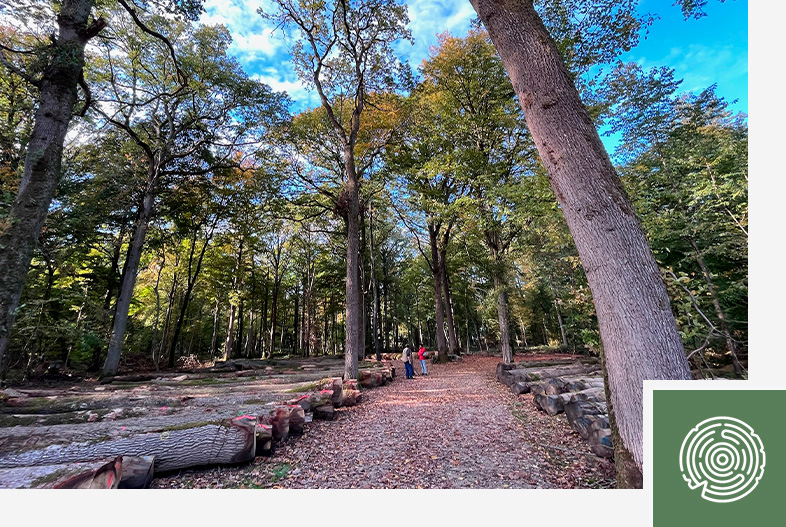
Sectioning and Sawing.
The initial processing phase involves sectioning the logs according to the desired lengths. For example, a 12-meter log can be sectioned into 4 parts of 3 meters or 3 parts of 4 meters depending on customer needs.
With our supervision of the process, it is possible to customize lengths up to 5 meters. Subsequently, the log is sawn longitudinally into 2, 3, or 4 parts, depending on the type of cutting and the designs desired on the wood (striped, semi-flamed, flamed).
Soaking Phase.
In the second phase, the logs are immersed in large tanks filled with water, and then cooked according to a precise boiling schedule.
Each wood species has different densities and therefore requires a specific boiling schedule, which differs in terms of temperatures and exposure times. This phase is very delicate as an inadequate water temperature or excessive soaking time could result in defective or discolored material.
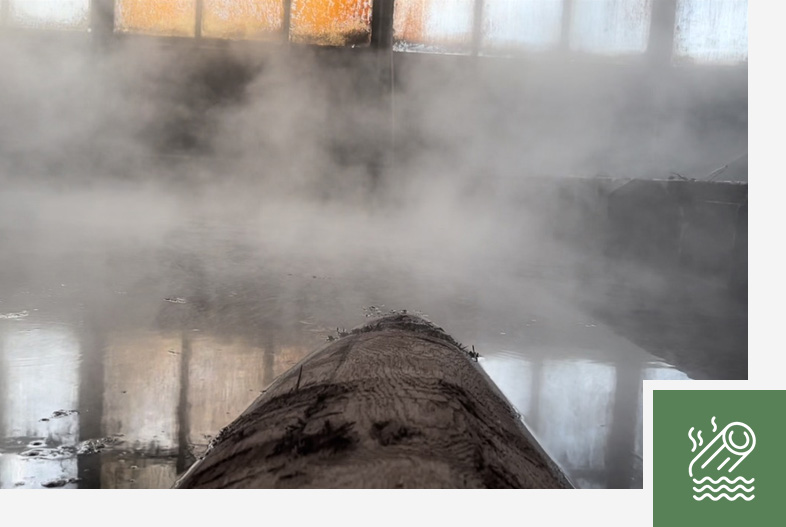
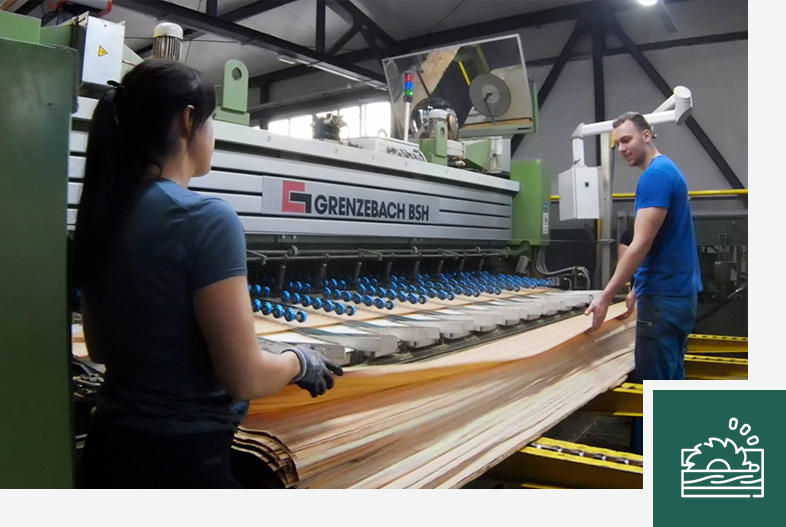
Slicing.
Once the veneer thickness is decided, the various sections of the log are sliced using various types of slicing machines. Slicers are essentially of 2 types: vertical or rotary. The vertical slicer is used for sections of ½ or 1/3 of the log to obtain the ‘flamed’ and ‘semi-flamed’ designs, while the rotary slicer is used for sections of ¼ of the log to obtain the striped design.
The slicing phase is crucial for technically perfect veneering, so we closely monitor the slicing of each produced sheet to ensure the absence of false thicknesses or marks due to dull blades. The most commonly sliced thickness is the commercial one of 0.56 mm, but customized thicknesses up to 40 mm are possible upon request.
Drying.
The sheets obtained from slicing are subjected to a drying process using a stretching dryer. This machinery is equipped with a metal net that transports the material inside where hot air dries the veneers.
At the end of the drying cycle, the wood is examined using a hygrometer to check the moisture level. If the material does not meet the required standards, it is reintroduced into the dryer for another cycle. The drying phase is crucial in ensuring optimal quality material, ready to meet the needs of our customers.
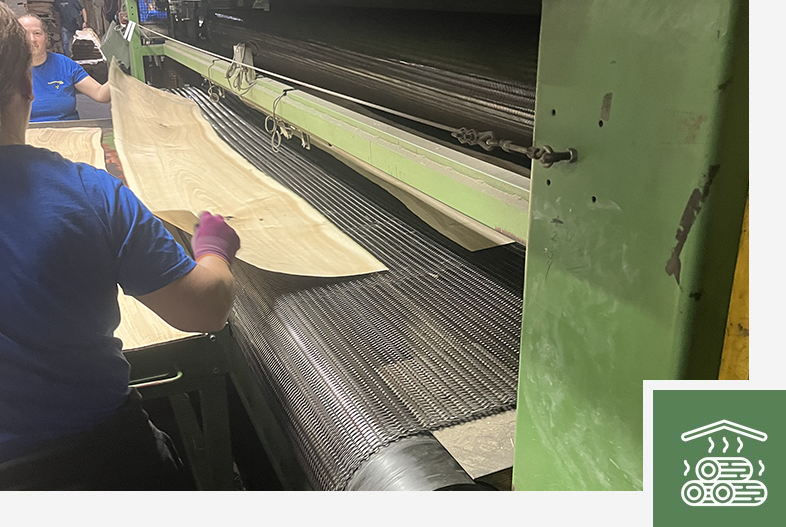
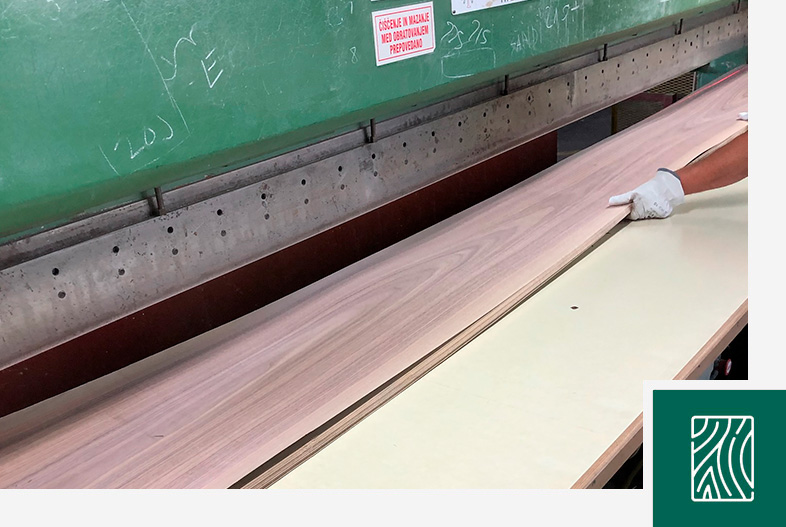
Trimming.
The final processing phase involves trimming the veneer using a longitudinal cutter.
This phase aims to eliminate wood defects such as knotholes and sapwood, making the product usable. In this phase, we pay close attention to the lengths and widths of the sliced material, in order to fully satisfy customer requirements.
Warehouse storage.
Once processing is finished, the veneers are divided and stored in our warehouses for subsequent selection and delivery to the customer.
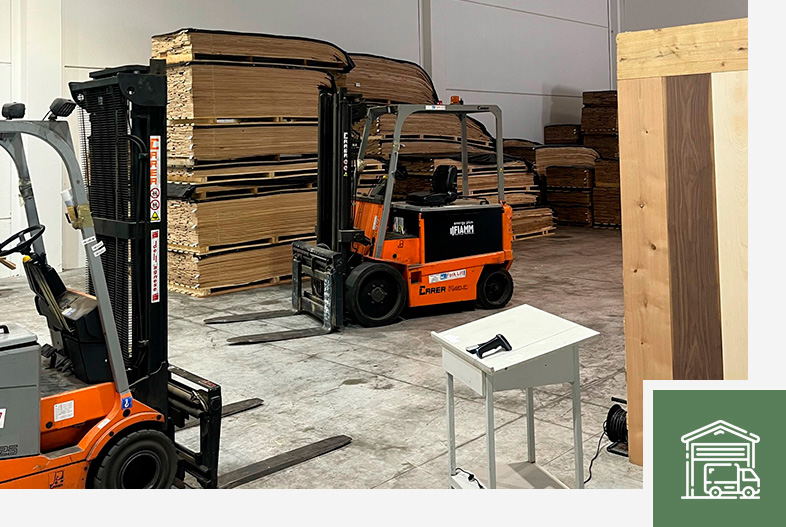
Log Veneers Srl
P. IVA 05290460269
Social Capital € 20.000,00 i.v.
privacy | cookies | credits QWeb Agency
Address
Via Castelfranco Veneto, 81/6
33170 Pordenone (Italy)
Contacts
Tel: + 39 0434.319172
Email: info@logveneers.com